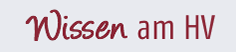
- DAZ.online
- DAZ / AZ
- DAZ 16/2012
- Sprühtrocknung – so ...
UniDAZ
Sprühtrocknung – so schnell kann Trocknen gehen!
EditorialLiebe Leserinnen, liebe Leser! Auf geht’s in die zweite Runde: Nachdem die UniDAZ-Rubrik im WS 2011/12 alle pharmazeutischen Fachdisziplinen einmal abgehandelt hat und Sie im März den spannenden Beitrag der UniDAZ-Wissenschaftspreis-Gewinnerin lesen konnten, beginnt nun mit dem Sommersemester die zweite Runde mit Fachbeiträgen aus allen Teildisziplinen der Pharmazie. Den Anfang macht in dieser Ausgabe die Pharmazeutische Technologie mit einem Grundlagenbeitrag zur Sprühtrocknung. Sie ist ein für die Pharmazie sehr wichtiges Verfahren, denn aufgrund der im Vergleich zu anderen thermischen Trocknungsverfahren niedrigen Temperaturbelastung des Materials können auch thermolabile Substanzen wie Peptide und Proteine sprühgetrocknet werden. Zudem eignen sich die pulverförmigen, meist freifließenden Endprodukte der Sprühtrocknung hervorragend für die direkte pharmazeutische Anwendung (z. B. als Pulver zur Inhalation oder zur Mikroverkapselung) wie auch zur Weiterverarbeitung in Granulations- oder Tablettierprozessen. Übrigens: Hinter der Marke "UniDAZ" verbirgt sich noch viel mehr als diese Reihe mit spannenden Fachbeiträgen für Pharmaziestudierende und alle Interessierten! So wird dieser Tage – pünktlich zum Semesterstart – auch die neueste Ausgabe des UniDAZ-Magazins an den Hochschulen verteilt. Wer kein Student mehr ist, sich aber trotzdem für die Beiträge des UniDAZ-Magazins interessiert, kann diese im Internet auf www.unidaz.de nachlesen und auch kommentieren. Und falls Sie Ihren Freunden und Kollegen zeigen wollen, dass Sie ein UniDAZ-Fan sind, dann klicken Sie einfach auf den "Gefällt mir"-Button der UniDAZ-Facebook-Seite. Viel Vergnügen und eine interessante Lektüre wünscht Ihre UniDAZ-Redaktion |
Die Sprühtrocknung ist eines der wichtigsten Verfahren zur Herstellung von Pulvern aus Lösungen, Suspensionen oder Emulsionen. Gut bekannt ist ihr Einsatz bei der Herstellung von Milchpulver, Instant-Kaffee oder -Tee. Aber auch in der pharmazeutischen Industrie ist die Sprühtrocknung von großer Bedeutung, z. B. zur Herstellung von Pulvern für die Inhalation, für die Mikroverkapselung oder auch für die Tablettierung. Leider wird die Sprühtrocknung in den pharmazeutischen Lehrbüchern noch sehr oberflächlich abgehandelt. Um diese Lücke zu schließen, gibt der folgende Beitrag eine Einführung in die verfahrenstechnischen Prozessschritte sowie die vielfältigen Systeme und Anwendungsbereiche der Sprühtrocknung.
Der Sprühtrocknungsprozess
Die Sprühtrocknung, auch häufig als Zerstäubungstrocknung bezeichnet, ist ein Schnellverdampfungs- oder Schnellverdunstungsverfahren, das auf der Trocknung kleinster Tröpfchen in einem temperierten Trocknungsgas, meist Luft, beruht. Als Sprühgut (Ausgangsmaterial für die Sprühtrocknung) dienen Lösungen, Suspensionen oder Emulsionen. In Abhängigkeit von den physikochemischen Eigenschaften der gelösten oder suspendierten Substanzen, dem Trocknerdesign sowie den Anforderungen an das Endprodukt, können Pulver (bestehend aus Einzelpartikeln), Agglomerate und sogar Granulate hergestellt werden. Prinzipiell gliedert sich das Verfahren in drei Hauptprozessschritte:
- die Zerstäubung des flüssigen Ausgangsmaterials in kleine Tröpfchen,
- die Trocknung der Tröpfchen im temperierten Luftstrom und
- die Trennung der trockenen Partikel von der Trocknungsluft.
Sprühtrocknungsanlagen sind hierbei so konstruiert, dass diese Prozesse kontinuierlich ablaufen und somit in relativ kurzer Zeit große Mengen produziert werden können, ohne dass die Anlage dabei gestoppt, neu beladen und wieder angefahren werden muss (Abb. 1).
Zerstäubung
Das Herzstück jeder Sprühtrocknungsanlage ist eine Zerstäubungs- oder Sprühdüse, deren Aufgabe es ist, die flüssige Formulierung in feine Tröpfchen zu zerstäuben und diese gleichmäßig in der Trocknungsluft des Sprühturmes zu verteilen. Das Versprühen führt zu einer enormen Vergrößerung der Gesamtoberfläche der Flüssigkeit, was hohe Trocknungsgeschwindigkeiten und extrem kurze Trocknungszeiten gewährleistet (Tab. 1).
Physikalisch betrachtet müssen beim Versprühen einer Flüssigkeit Kräfte überwunden werden, die den Zusammenhalt der Flüssigkeitsmoleküle im Tropfeninneren bewirken und versuchen, dem Volumen die kleinste mögliche Oberfläche zu geben. Die wichtigsten Größen sind hierbei die Viskosität und die Oberflächenspannung der zu versprühenden Formulierung. Für die Sprühtrocknung steht eine ganze Reihe von Düsen zur Verfügung, die nach unterschiedlichen physikalischen Prinzipien arbeiten (Abb. 2).
Tab. 1: Sprühtrocknung: Zusammenhang zwischen Tropfengröße (Radius) und Gesamtoberfläche von 1 Liter versprühter Flüssigkeit mit der ungefähren Trocknungszeit eines Tropfens (nach Stahl 1980) | ||
Radius |
Oberfläche |
Trocknungszeit |
1 µm |
6000 m2
|
0,0001 s |
10 µm |
600 m2
|
0,01 s |
100 µm |
60 m2
|
1,0 s |
1000 µm |
6 m2
|
100 s |
Rotationszerstäuber
Rotationszerstäuber verwenden eine schnell rotierende Scheibe, um den Flüssigkeitsstrom in einzelne Tröpfchen "aufzubrechen". Die Flüssigkeit wird hierbei in der Mitte der Scheibe aufgetragen und durch die Zentrifugalkraft nach außen zum Scheibenrand beschleunigt. Dort wird der sich bildende Flüssigkeitsfilm in feine Tröpfchen zerrissen. Die Tropfengröße ist vor allem von der Rotationsgeschwindigkeit der Scheibe, aber auch von der Förderrate des Sprühgutes sowie von dessen Viskosität und Oberflächenspannung abhängig. Rotationsscheiben haben in der Regel einen Durchmesser von 5 bis 50 cm und drehen sich mit einer Geschwindigkeit von 5000 bis 40.000 Umdrehungen pro Minute. Systematische Untersuchungen haben gezeigt, dass die erzeugte Tropfengröße annähernd umgekehrt proportional zur peripheren Rotationsgeschwindigkeit der Scheibe ist. Rotationszerstäuber können Sprays mit einer mittleren Tropfengröße von 15 bis 250 µm erzeugen. ZIhr großer Vorteil gegenüber anderen Düsensystemen liegt vor allem in den hohen Durchsatzmengen, die sich von 10 l/h im Laborbereich auf bis zu 200.000 l/h im Produktionsmaßstab erstrecken können.
Einstoffdüsen
Einstoffdüsen (engl. "pressure nozzles") pressen die zu zerstäubende Flüssigkeit bei einem hohen Druck von etwa 50 bis 150 bar durch ein enges Lumen in der Düse. Hierbei wird gemäß dem Bernoulli-Prinzip der hohe statische Druck in kinetische Energie umgewandelt und die Flüssigkeit somit stark beschleunigt. In der sogenannten Drallkammer wird der Flüssigkeitsstrom dann zusätzlich noch in eine spiralig rotierende Bewegung versetzt. Beim Austritt aus der Düsenöffnung, die in der Regel einen Durchmesser von 0,5 bis 3,0 mm hat, zerreißt der beschleunigte Flüssigkeitsstrom dann in einzelne Tröpfchen.
Die Tropfengröße ist bei diesem Düsensystem anhängig vom Druckverlust, dem Durchmesser der Düsenöffnung sowie selbstverständlich auch von der Viskosität und Oberflächenspannung des Sprühgutes. Ein höherer Druckverlust und eine kleinere Düsenöffnung erzeugen kleinere Tropfendurchmesser. Im Gegensatz zu Rotationszerstäubern ist die Durchsatzmenge aufgrund der Düsenöffnung jedoch meist stark limitiert. In der Literatur werden Werte von bis zu 750 l/h angegeben.
Vorteile und Nachteile der SprühtrocknungVorteile
Nachteile
|
Zweistoff- und Mehrstoffdüsen
Zweistoffdüsen verwenden ein Gas (meist Luft oder Stickstoff) zum Zerstäuben des Sprühguts. Sie bestehen aus zwei ineinander geschobenen konzentrischen Röhren, wobei die Flüssigkeit meist durch die innere Röhre und das Zerstäubungsgas über die außen liegende Röhre zugeführt wird. Der große Vorteil von Zweistoffdüsen ist, dass sie bei wesentlich niedrigeren Drücken (etwa 1,5 – 10 bar) arbeiten und je nach Düsendesign eine relativ enge Tropfengrößenverteilung gewährleisten können. Die mittlere Tropfengröße hängt dabei vor allem vom Verhältnis der Flussgeschwindigkeiten des Zerstäubungsgases und des Sprühgutes ab. Mit zunehmendem Druck und somit zunehmendem Fluss an Zerstäubungsgas wird die Tropfengröße geringer. Gleiches gilt bei abnehmender Fördergeschwindigkeit der Sprühflüssigkeit. Zudem spielen auch hier die Viskosität und Oberflächenspannung des Sprühgutes wieder eine wichtige Rolle hinsichtlich der möglichen Tröpfchengrößen.
Dreistoffdüsen (Gas/Flüssig/Gas oder Flüssig/Gas/Flüssig) oder auch Vierstoffdüsen sind häufig Spezialausführungen, die beispielsweise zur Zerstäubung mit gleichzeitiger Mischung von Flüssigkeiten eingesetzt werden. Dies kann etwa für die In-situ-Mikroverkapselung von Interesse sein, bei der das zu verkapselnde, meist wässrig formulierte Gut erst an der Düsenspitze mit der organischen Polymerlösung in Kontakt gebracht wird.
Ultraschalldüsen
Ultraschalldüsen zerstäuben das Sprühgut durch hochfrequente Vibrationen des Düsenkopfes, meist im Bereich zwischen 25 bis 120 kHz. Das Herzstück der Düse sind zwei Piezokristalle, die sich aufgrund eines von außen angelegten elektrischen Wechselfeldes ständig in ihrer räumlichen Ausdehnung verändern. Hierbei wird die elektrische Energie in mechanische Energie umgewandelt, welche auf den Düsenkopf übertragen wird. Die zu versprühende Flüssigkeit wird durch eine Kapillare zum Düsenkopf geführt und dort durch die erzeugten Vibrationen in feine Tröpfchen zerstäubt.
Die Tropfengröße ist hier in erster Linie von der Frequenz der Düse abhängig: Mit steigender Frequenz werden die Tropfen kleiner. Es ist allerdings zu beachten, dass jede Ultraschalldüse durch ihren Aufbau eine bestimmte Resonanzfrequenz besitzt, bei der sie betrieben wird. Dies bedeutet, dass je nach gewünschter Tropfengröße eine andere Ultraschalldüse verwendet werden muss. Im Gegensatz zu den zuvor besprochenen Düsen haben Viskosität, Oberflächenspannung und Fördergeschwindigkeit der zu versprühenden Flüssigkeit hier nur eine untergeordnete Bedeutung hinsichtlich der Tropfengröße. Im Vergleich zu Ein- und Zweistoffdüsen erzeugen Ultraschalldüsen ein sogenanntes "Soft Spray", das durch eine niedrige Austrittsgeschwindigkeit der Tropfen am Düsenkopf gekennzeichnet ist.
Trocknung
Bei der Sprühtrocknung handelt es sich um ein konvektives Trocknungsverfahren, bei dem die Wärmeenergie eines Trocknungsgases, meist heiße trockene Luft, auf die zerstäubte flüssige Formulierung übertragen wird. Das Lösungs- oder Dispersionsmittel des Sprühgutes verdampft dabei fast gleichzeitig mit der Zerstäubung.
Wärme- und Stoffübergang
Generell hängt die Effektivität des Trocknungsverfahrens von zwei Parametern ab:
1. Geschwindigkeit des Wärmetransports vom Trocknungsgas in das (kältere) Sprühgut, wobei die Temperaturdifferenz ΔT zwischen beiden entscheidend ist.
2. Geschwindigkeit des Stofftransports aus dem Sprühgut in das Trocknungsgas, wobei die Differenz zwischen dem (höheren) Dampfdruck dp im Sprühgut und dem (niedrigeren) Partialdampfdruck im Trocknungsgas entscheidend ist.
Die Trocknungseffektivität der Sprühtrocknung ist durch zwei Besonderheiten, die aus der Zerstäubung der Flüssigkeit resultieren, höher als bei anderen Verfahren:
Die Vergrößerung der Gesamtoberfläche führt zu einer starken Erhöhung der Diffusionsgeschwindigkeit der Lösemittelmoleküle beim Übergang aus der flüssigen Phase in die Gasphase (Ficksches Diffusionsgesetz).
Die kleinere Tropfengröße korreliert mit einer größeren Krümmung der Oberfläche, die den Dampfdruck steigen lässt. Gemäß der Kelvinschen Gleichung steigt der Dampfdruck p eines Tropfens mit der Abnahme des Tropfenradius an: (Formel s. hier)
Diese beiden wichtigen Vorteile der Sprühtrocknung im Vergleich zu anderen thermischen Trocknungsverfahren lassen sich also wie folgt zusammenfassen:
Die Oberflächenvergrößerung führt zu einem extrem schnellen Wärme- und Stoffaustausch zwischen Trocknungsgas und Tropfen.
Der geringe Tropfenradius erhöht den Dampfdruck der Flüssigkeit im Tropfen und senkt somit deren Siedepunkt.
Trocknungskinetik
Der Verlauf der Trocknung von Lösungen und Suspensionen kann bei der Sprühtrocknung in zwei aufeinanderfolgende Abschnitte eingeteilt werden. Zur Veranschaulichung soll hier eine wässrige Zuckerlösung betrachtet werden. Im ersten Trocknungsabschnitt wird das anfänglich in großer Menge vorliegende und an der Tropfenoberfläche frei vorhandene Lösemittel (Wasser) entfernt. Dadurch nimmt der Durchmesser des Tropfens ab, und die Zuckerlösung konzentriert sich immer weiter auf (Abb. 3). Die Trocknungsgeschwindigkeit ist konstant, solange die Oberfläche des Tropfens komplett mit Wasser belegt ist. Im Englischen wird dieser erste Trocknungsabschnitt daher auch als "Constant Rate" bezeichnet (Beispiel im Textkasten). Die Temperatur der Tropfenoberfläche ist ebenfalls konstant und wegen der Verdunstungskälte relativ niedrig. Der englische Ausdruck "Wet bulb temperature" für die Oberflächentemperatur des Tropfens im ersten Trocknungsabschnitt wird im Deutschen meist als Kühlgrenztemperatur bezeichnet.
ZahlenbeispielEin Wassertropfen, der in Luft bei Normaldruck (1013 mbar) mit einer Temperatur von 100 °C und einer relativen Feuchte von 1% getrocknet wird, hat eine Oberflächentemperatur von nur etwa 35 °C. Bei dieser Temperatur herrscht an der Tropfenoberfläche ein Sättigungsdampfdruck von ungefähr 56 mbar. Der Partialdruck des Wasserdampfes in der Trocknungsluft bei 100 °C und 1% relativer Feuchte beträgt aber lediglich um die 10 mbar. Dies zeigt deutlich, dass die Voraussetzungen für die Sprühtrocknung – nämlich der Wärmetransport von der Trocknungsluft zum Tropfen, wie auch der Stofftransport von der Tropfenoberfläche in die Trocknungsluft – erfüllt sind. |
Mit fortschreitender Trocknung und Aufkonzentrierung der Zuckerlösung wird irgendwann ein Punkt erreicht, an dem die Migration von Wassermolekülen zur Tropfenoberfläche den geschwindigkeitsbestimmenden Schritt darstellt. Die komplette Befeuchtung der Oberfläche mit Wasser kann nicht mehr aufrechterhalten werden, und es kommt zur Krustenbildung durch den Feststoff an der Oberfläche (Abb. 3). An diesem Punkt, der den Übergang vom Tropfen zum Partikel kennzeichnet, befindet sich aber noch immer Feuchtigkeit im Inneren des Partikels, die dann im zweiten Trocknungsabschnitt entfernt wird. Die noch vorhandenen Wassermoleküle diffundieren von innen nach außen zur Oberfläche, wo sie verdunsten, aber die Trocknungsgeschwindigkeit wird mit fortschreitender Trocknung immer langsamer, was der immer dicker werdenden Kruste geschuldet ist. Der zweite Trocknungsabschnitt heißt deshalb auf Englisch "Falling Rate". Mit dem Erreichen einer Gleichgewichtsfeuchte (Restfeuchte) ist die Trocknung schließlich beendet.
Im zweiten Trocknungsabschnitt nimmt der Durchmesser des Partikels meist nicht weiter ab. Seine Oberflächentemperatur steigt mit sinkender Trocknungsgeschwindigkeit, bis sie schließlich die Temperatur des Trocknungsgases erreicht hat. Das Trocknungsgas selbst kühlt sich während des Trocknungsvorganges zunehmend ab, da ja ein Teil der Wärmeenergie zur Verdampfung des Lösemittels aufgewendet wurde. Der Übergang vom ersten zum zweiten Trocknungsabschnitt der Sprühtrocknung ist in der Regel durch einen deutlichen Knick in der Kurve der Trocknungsgeschwindigkeit gegen die Zeit gekennzeichnet (Abb. 4).
Partikelmorphologie
Mit dem zunehmenden Feststoffgehalt eines Tropfens, der sowohl von dessen Masse als auch von der Konzentration der Lösung abhängt, wächst auch die Größe des durch die Sprühtrocknung erhaltenen Partikels. In der Literatur findet sich hierzu eine einfache Gleichung, die diesen Zusammenhang quantitativ beschreibt: (Gleichung s. hier)
Darüber hinaus hat aber auch die Trocknungsgeschwindigkeit einen merklichen Einfluss auf die Größe des Partikels: Je höher die Trocknungsgeschwindigkeit ist, desto größer werden auch die Partikel, sodass ihre Dichte (bei gleich bleibender Masse) sinkt. Dies hängt vor allem mit dem Zeitpunkt der Krustenbildung zusammen. Bei hohen Trocknungsgeschwindigkeiten kommt es schnell zur Krustenbildung, da die schnelle Verdampfung an der Tropfen-oberfläche nur sehr kurze Zeit durch die Diffusion der Flüssigkeitsmoleküle kompensiert werden kann. In diesem frühen Stadium ist der Tropfen noch relativ groß.
Zusätzlich spielen auch die Substanzeigenschaften selbst eine wichtige Rolle hinsichtlich der finalen Partikelgröße und der Partikelmorphologie.
Partikelgewinnung (Trennung)
Im letzten Prozessschritt der Sprühtrocknung müssen die getrockneten Partikel noch aus dem Trocknungsgas entfernt werden. Größere und schwere Partikel lagern sich häufig aufgrund ihrer Trägheit in Auffanggefäßen am unteren Ende des Trocknungsturmes ab. Feinere Partikel folgen jedoch dem Gasstrom und müssen daraus mit Partikelabscheidern entfernt werden. Am häufigsten werden Zyklonabscheider, elektrostatische Partikelkollektoren oder auch großflächige Filtereinheiten verwendet. Industriell werden aufgrund ihrer einfachen und ökonomischen Arbeitsweise vor allem Zyklonabscheider (= Fliehkraftabscheider) eingesetzt.
Ein normaler Zyklonabscheider kann in vier Bereiche eingeteilt werden (Abb. 5): den Einlaufzylinder, den Kegel, den Partikelauffangbehälter und das Tauchrohr. Im Einlaufbehälter wird das Gemisch aus Trocknungsgas und Partikeln durch die tangentiale Anordnung des Einlasses auf eine kreisförmige Bahn gebracht. Durch die anschließende Verkleinerung des Durchmessers im Kegel nimmt die Drehgeschwindigkeit stark zu. Die Partikel werden durch die Fliehkraft an die Kegelwand gepresst und an dieser so weit abgebremst, dass sie sich aus der schnell weiterrotierenden Gasströmung lösen und nach unten in den Partikelauffangbehälter rieseln. Das von den Partikeln befreite Trocknungsgas verlässt den Kegel nach oben durch das zentral angeordnete Tauchrohr.
Kritische Prozessparameter der Sprühtrocknung
In modernen Sprühtrocknungsanlagen lassen sich fast alle Prozessparameter, die die Trocknung beeinflussen, messen und kontrollieren. Dazu gehören die Fördergeschwindigkeit und die mittlere Tropfengröße der versprühten Flüssigkeit sowie die Temperatur, absolute Feuchte und Durchflussgeschwindigkeit des Trocknungsgases. Es gilt allerdings zu beachten, dass jeder dieser Parameter nur in bestimmten Bereichen variiert werden kann, damit stets eine ausreichende Trocknung der Partikel gewährleistet bleibt. Zum Beispiel muss die Temperatur der Trocknungsluft am Ende des Trocknungsturmes noch ausreichend hoch sein, damit eine Kondensation des entfernten Lösemittels im Bereich der Partikelabscheidung vermieden wird.
Zur Prozesskontrolle verfügen die meisten Systeme über diverse Sensoren, die die Temperatur und den Feuchtigkeitsgehalt des Trocknungsgases am Einlass (Inlet) und am Auslass (Outlet) der Trocknungskammer messen. Die Fördergeschwindigkeit des Sprühgutes kann stufenlos durch Pumpen geregelt und die mittlere Tropfengröße durch die Wahl einer geeigneten Düse festgelegt werden.
Die kritischen Eigenschaften der Prozessparameter seien hier kurz zusammengefasst:
- Einlasstemperatur (Inlet Temperature)
Je heißer und trockener die zugeführte Trocknungsluft ist, desto höher ist die Trocknungsgeschwindigkeit. Hohe Temperaturen bedeuten aber trotz der oben beschriebenen Tatsache, dass sich am Tropfen aufgrund der Verdunstungskälte eine niedrige Temperatur einstellt, stets auch eine höhere thermische Belastung für das zu trocknende Gut.
- Auslasstemperatur (Outlet Temperature)
Die Auslasstemperatur ist die Temperatur der Trocknungsluft am Ausgang aus der Trocknungskammer. Sie ist niedriger als die Einlasstemperatur und hängt von mehreren Variablen ab: Einlasstemperatur und Flussrate des Trocknungsgases sowie verdampfte Flüssigkeitsmenge, die wiederum von der Sprühgeschwindigkeit und der Beschaffenheit der Lösung abhängt.
- Flussrate des Trocknungsgases
Erhöht man die Flussrate des Trocknungsgases, steht mehr Gas pro Zeiteinheit für die Trocknung zur Verfügung. Somit kann pro Zeiteinheit auch mehr Flüssigkeit verdampft werden. Allerdings führt eine Erhöhung der Flussrate des Trocknungsgases im Gegenzug zu einer Verringerung der Verweilzeit der Tropfen bzw. Partikel im Trocknungsturm, sodass große Partikel unter Umständen nicht ausreichend trocken werden.
- Sprühgeschwindigkeit
Ungeachtet von der Bedeutung der Sprühgeschwindigkeit für die Partikelgröße, führt eine Erhöhung dieses Parameters dazu, dass im Trocknungsturm pro Zeiteinheit und Volumen an Trocknungsgas mehr Flüssigkeit verdampft werden muss, um trockene Partikel zu erhalten.
- Sprühguteigenschaften
Natürlich beeinflussen auch die Eigenschaften des Sprühgutes den Trocknungsprozess, die Partikelbildung und die Partikelmorphologie. Wichtige Parameter sind hierbei der Dampfdruck des Lösemittels und die Konzentration der gelösten oder suspendierten Bestandteile. Einige Materialien können schnell an der Tropfenoberfläche eine "Haut" bilden, was die Trocknungsgeschwindigkeit bremst und eventuell das Trocknungsergebnis verschlechtert, d. h. die Partikel sind nicht trocken genug.
Varianten des Sprühtrocknungsprozesses
Bei der industriellen Sprühtrocknung lassen sich hinsichtlich Gasführung und Produktbewegung prinzipiell drei Systeme unterscheiden (Abb. 6):
- das Gleichstromverfahren (Co-Current),
- das Gegenstromverfahren (Counter-Current) sowie
- Mischverfahren (Mixed).
Beim Gleichstromverfahren wird das Trocknungsgas in Sprührichtung zugeführt. Hierbei trifft die wärmste Trocknungsluft auf die gerade versprühte Flüssigkeit, das heißt auf die Tropfen mit dem höchsten Feuchtigkeitsgehalt. Durch den Verlust der für die Verdunstung/Verdampfung benötigten Wärmeenergie kühlt sich der Tropfen auf die Wet Bulb Temperatur ab und wird somit schonend getrocknet.
Beim Gegenstromverfahren wird das Trocknungsgas entgegengesetzt der Sprührichtung zugeführt. Die Verweilzeit der Tropfen im Trocknungsturm ist länger, und es lassen sich größere Partikel herstellen. Allerdings treffen die nahezu trockenen Partikel auf die wärmste Trocknungsluft, was zu einer hohen Temperaturbelastung führt. Temperatursensitive Güter sollten daher im Gleichstromverfahren getrocknet werden.
Neben diesen beiden Verfahren findet man vereinzelt noch sogenannte Mischverfahren, die vor allem zur Herstellung grober Pulver am Übergangsbereich zwischen Gleich- und Gegenstromverfahren verwendet werden.
Open-Loop- und Closed-Loop-Systeme
In industriellen Sprühtrocknungsanlagen werden meistens wässrige Formulierungen verarbeitet, wozu das Open-Loop-System sich am besten eignet (Abb. 7a). Als Trocknungsgas dient meistens Umgebungsluft, die zuerst mittels einer Heizung und eines Entfeuchters auf die gewünschte Temperatur und niedrige relative Luftfeuchte gebracht wird. Darauf durchströmt sie den Sprühtrockner und wird nach dem Passieren eines Abluftfilters in der Regel ins Freie befördert. Wenn das Sprühgut organische Lösemittel enthält, muss es aufgrund der Entflammbarkeit und des Explosionsrisikos mit einem inerten Gas (häufig: Stickstoff) in einem Closed-Loop-System sprühgetrocknet werden (Abb. 7b); dabei muss der Sauerstoffgehalt im System so niedrig wie möglich sein. Auch hier wird das Trocknungsgas zuerst auf die gewünschte Temperatur und Feuchte gebracht. Nach der Sprühtrocknung und Partikelabscheidung wird es einem Kondensator zugeführt, in dem das verdampfte organische Lösemittel rückgewonnen wird. Der vom Lösemittel gereinigte Stickstoff wird schließlich wieder der Sprühtrocknungsanlage zugeführt, in der er erneut erwärmt wird und den nächsten Trocknungszyklus durchläuft.
AutorDr. rer. nat. Heiko A. Schiffter studierte Pharmazie an der Universität Heidelberg und wurde anschließend am Lehrstuhl für Pharmazeutische Technologie und Biopharmazie der Universität Erlangen promoviert. Von 2006 bis 2008 war er Bellhouse Research Fellow am Department of Engineering Science der Universität Oxford in Großbritannien, von 2008 bis 2009 Brasenose Research Fellow in Biomedical Engineering. Seit 2009 ist er Lecturer in Engineering Science und verantwortlich für den Bereich Drug and Vaccine Delivery am Institute of Biomedical Engineering der Universität Oxford. Kontakt: heiko.schiffter@gmail.com |
Quellen und weiterführende Literatur
Aulton ME (2007). Pharmaceutics – The Design and Manufacture of Medicines, 3rd revised edition. Churchill Livingstone.
Blei S, Sommerfeld M (2005). Sprühtrocknung – Einfluss der Elementarprozesse auf Produkteigenschaften. Chemie Ingenieur Technik 77(3):278 – 282.Buchi (2012). www.buchi.ch/Spray-Drying-Encapsulation.69.0.html.Gablenz S (2001). Sprühtrocknung und Sprühhydrolyse – neue Methoden zur Herstellung von Metalloxiden und zur Modifizierung von BaTiO3 • Diss. Univ. Halle-Wittenberg. GEA Niro (2012). www.niro.com/spray-drying-process.html.Grassmann P, et al (1997). Einführung in die thermische Verfahrenstechnik. Walter de Gruyter, Berlin.Lee G (2002). Spray-drying of proteins. In Carpenter JF, Manning MC, eds. Rational Design of Stable Protein Formulations – Theory and Practice. Pharm Biotechnol 13:135 – 158. Maa Y-F, et al (1998). Spray-Drying Performance of a Bench-Top Spray Dryer for Protein Aerosol Powder Preparation. Biotechnol Bioeng 60(3): 301 – 309. Masters K (1991). Spray Drying Handbook, 5th edition. Longman Scientific & Technical, Essex.Masters K (2002). Spray Drying in Practice. SprayDryConsult International ApS, Charlottenlund.Rähse W, Dicoi O (2009). Produktion disperser Stoffe: Industrielle Sprühtrocknung. Chemie Ingenieur Technik 81(6):699 – 716.Sono-Tek Ultrasound Nozzles. www.sono-tek.com/ultrasonic-nozzle-technology. Stahl PH (1980). Feuchtigkeit und Trocknen in der pharmazeutischen Technologie. Dr. Dietrich Steinkopff Verlag, Darmstadt.Stieß M (1994). Mechanische Verfahrenstechnik 2. Springer, Berlin.Stieß M (2007). Mechanische Verfahrenstechnik – Partikeltechnologie 1, 3. Auflage. Springer, Berlin.
UniDAZ kostenlosWenn Sie Pharmazie studieren oder gerade im Praktischen Jahr sind, können Sie sich das UniDAZ-Magazin und die zehn Ausgaben der DAZ, in denen die Rubrik UniDAZ erscheint, auch kostenlos nach Hause schicken lassen. Melden Sie sich einfach bei uns: service@deutscher-apotheker-verlag.de oder Tel. (07 11) 25 82-3 41 |
Literaturtipp
Das Schicksal der Arzneistoffe
Diese Einführung in die Pharmakokinetik legt den Schwerpunkt auf kinetische Modelle und mathematische Berechnungen. Der Autor erläutert die Grundlagen der Resorption, Verteilung, Metabolisierung und Ausscheidung von Wirkstoffen. Mithilfe von mathematischen Funktionen beschreibt er die Gesetzmäßigkeiten, mit denen sich Wirkstoffkonzentrationen im Organismus ändern. Das Buch enthält 20 Übungsaufgaben mit Musterlösungen zur Verknüpfung der Theorie mit praktischen Fallbeispielen.
Heiko A. Schiffter
Pharmakokinetik – Modelle und BerechnungenXII, 148 S., 52 s/w Abb., 25 Tab., 323 mathematische Formeln. Kart. 54,– Euro
Wissenschaftliche Verlagsgesellschaft, Stuttgart 2009ISBN 978-3-8047-2536-2
Bauer/Frömming/Führer in neuer Auflage
Unter der Federführung von drei erfahrenen Hochschullehrern erhielt dieser Lehrbuch-Klassiker eine neue Gestalt. Jetzt erleichtern didaktische Elemente, farbiges Design und viele neue Abbildungen das Studium. Aktualisiert wurden die Kapitel über
- physikalisch-chemische Grundlagen der Arzneiformung
- technologische Verfahren und Grundoperationen
- spezielle Arzneiformen
Hinzugekommen sind Kapitel über kindgerechte Arzneiformen, Medizinprodukte/Verbandstoffe und biotechnologische Themen.
Kurt H. Bauer (Begr.), Karl-Heinz Frömming (Begr.), Claus Führer (Begr.), Bernhard C. Lippold (Bearb.), Christel Müller-Goymann (Bearb.), Rolf Schubert (Bearb.)
Lehrbuch der Pharmazeutischen TechnologieMit einer Einführung in die Biopharmazie
9. Aufl., 784 Seiten. Gebunden 79,– Euro
Subskriptionspreis bis 31.05.2012: 64,– Euro
Wissenschaftliche Verlagsgesellschaft, Stuttgart 2012 ISBN 978-3-8047-2552-2
Einfach und schnell bestellen• Per Post: Deutscher Apotheker Verlag, Postfach 10 10 61, 70009 Stuttgart • Per Telefon: 0711 – 2582 341 • Per Fax: 0711 – 2582 290 • Per Freecall: 0800 – 2990 000 (zum Nulltarif mit Bandaufzeichnung) • Per E-Mail: service@deutscher-apotheker-verlag.de • Im Internet: www.buchoffizin.de |
0 Kommentare
Das Kommentieren ist aktuell nicht möglich.