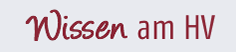
- DAZ.online
- DAZ / AZ
- DAZ 26/2009
- Zement – vom Klimasü...
DAZ wissenswert
Zement – vom Klimasünder zum Klimaretter?
Zement ist steingewordene Idee. Er steht für grandiose Architektur wie für seelenlose Plattenbauten. Römerzement ist die Frühform dieses universalen Baustoffes. Noch Ende des 19. Jahrhunderts rühmte man seine Härte und vermutete, die Römer hätten ihn mit Salz oder Zucker angerührt. Tatsächlich verfuhren die Römer jedoch so: Sie mischten Puzzolan- und Ziegelmehl, Sand und gebrannten Kalk und stampften den Mörtel mit Bruch- oder Backsteinen in Schalungen. Die Mauer (lat. murus) ersetzte so die griechische Säule als wesentliches Element der Architektur.
Die Römer bauten das Fundament des Kolosseums (Amphitheatrum Flavium) für 50.000 Besucher (72 – 80 n. Chr.) in sumpfigem Boden und schufen mit den Aquädukten die Lebensadern ihrer Städte. Das von Kaiser Hadrian um 120 auf dem Marsfeld erbaute Pantheon ist bis heute ein grandioses Zeugnis römischer Betonbaukunst. Die Kuppel spannt sich über 43 Meter. Um ihr Gewicht möglichst niedrig zu halten, erfanden seine Baumeister Zuschlagstoffe. Den unteren Ringen gaben sie Ziegelbruch zu, den mittleren Tuff, den oberen Bims und dem letzten Ring um den offenen Okulus leere Amphoren. Eine größere Kuppel aus Beton wagte man erst 1913. Der Stettiner Architekt Max Berg (1870 – 1947) baute die Jahrhunderthalle in Breslau mit einer Spannweite von 65 m, die seit 2006 zum Weltkulturerbe zählt. Sie besteht allerdings aus Stahlbeton.
Mühsam neu erfunden
Die Römer nannten Gebäude aus Gussmörtel "opus caementitium". Heute meint der Begriff Zement nur das Bindemittel. Kommt Wasser dazu, spricht man von Mörtel. Mit Sand oder Kies gemischt, wird er zu Beton. Als die Germanen im 5. Jahrhundert die Aquädukte Roms zerstörten, ging mit dem Römischen Weltreich auch das Wissen um den Zement verloren. Die Baumeister des Abschnitts I des Speyerer Doms (1030 – 1061) schafften es beispielsweise nicht, das auf 14 m Spannweite geplante Tonnengewölbe mit Stein zu bauen. Sie mussten auf Holz ausweichen.
Das Geheimnis, das Rom zur Ewigen Stadt gemacht hat, war der Puzzolan, eine sandige Vulkanasche aus Puteoli (heute Pozzuoli) bei Neapel. Er machte den Römerbeton steinhart und wasserdicht. Ganz verloren ging das Wissen wohl nicht, denn Raffael (1483 – 1520) beschwerte sich 1515 bei Papst Leo X., dass viele seiner Vorgänger nach Puzzolan haben graben lassen und dabei Fundamente unterhöhlt und Tempel und Statuen zerstört haben.
Puzzolan gibt es nördlich der Alpen nicht. Eher zufällig entdeckten die Holländer die ähnlich gute hydraulische Wirkung – Festwerden bei Wasserzugabe – von rheinischem Trass, einem in der Eifel vorkommenden vulkanischen Tuff. Als dann 1824 der Maurer Joseph Aspdin (1778 – 1855) die richtige Mischung des heute noch sehr wichtigen Portlandzementes gab und ein Patent darauf einreichte, bedeutete dies einen enormen Fortschritt. Den Namen hatte er aus der grauen Farbe der Felsen seiner Heimat, der südenglischen Halbinsel Portland, abgeleitet. Die englische Zementindustrie wurde Weltspitze.
Das erste deutsche Zementwerk hatte 1838 zwar der Apotheker Ernst Gustav Leube (1808 – 1881) in Ulm errichtet. Als Vater des deutschen Portlandzements gilt aber der Chemiker Hermann Bleibtreu (1824 – 1881), ein Schüler Justus Liebigs (1803 – 1873). Er hatte die streng geheimen Rezepte der britischen Zementmetropolen ausspioniert und systematisch weiterentwickelt. 1852 nahm er in Züllchow bei Stettin sein erstes Werk für Portlandzement in Betrieb.
Zum Durchbruch verhalf dem Zement aber ein französischer Gärtner: Joseph Monier (1823 – 1906) hatte mit dünnen Eisendrähten seine selbst gegossenen Betonkübel verstärkt und damit den Eisenbeton erfunden. Ein neues Zeitalter des Bauens begann.
"Beton ist fließender Fels. "
Peter Ustinov (1921 – 2004)
Vergebliche MüheBeim Bau des Wiener Stephansdoms um 1450 wurde dem Mörtel vergebens Heuriger zugegeben, um die Festigkeit zu erhöhen. |
Portlandzement wird bei 1450 °C gebrannt
Zement wird aus einem Gemisch von Kalkstein mit geringeren Anteilen Ton, Mergel, Sand und Eisenerz hergestellt. Deshalb stehen Zementfabriken immer in der Nähe von Kalksteinbrüchen. Die fein gemahlenen Rohstoffe werden in Drehrohröfen bei 1450 °C zu Zementklinker (kurz: Klinker) gesintert. Die walnussgroße Stücke werden mit Gips (CaSO4 • 2 H2 O) oder Anhydrit (CaSO4) und eventuell weiteren Zuschlag- und Ergänzungsstoffen vermahlen.
Das Brennen erfolgt innerhalb des sich drehenden Ofenrohrs bei ansteigenden Temperaturen. Bei 700 °C verdampft das noch enthaltene Wasser, und die Tonminerale werden zu aktiven Oxiden, insbesondere Tonerde (Al2 O3). Bei 1250 °C zerfällt das Calcit (CaCO3) in Kohlendioxid und Branntkalk (CaO), der mit Quarz (SiO2) und Tonerde zu Ca2 SiO4 , Ca2 Al2 O7 und Ca12 Al14 O33 reagiert. Bei der Sintertemperatur von 1450 °C zerfallen die Alumosilicatverbände der Tonmineralien zu Inselsilicaten und Aluminaten. Das schnelle Abkühlen auf unter 200 °C verwandelt sie in die Klinkermineralien Alit, Belit, Aluminat und Ferrit (Tab. 1).
Die Verwandlung des Zementpulvers in harten Stein hat ein wenig von Zauberei. Denn der Vorgang ist noch immer nicht vollständig aufgeklärt. Wasser hydratisiert Alit und Belit. Es bilden sich an den Partikeloberflächen die wichtigen Calciumsilicathydratphasen (C-S-H). Das sind kleine Kristallnadeln, die immer weiterwachsen, etwa wie kleine Seeigel, deren Stachelkleid immer länger wird. Schließlich wachsen die Seeigel ineinander und bilden ein festes Kristallgerüst.
Die C-S-H sind die elementaren Nanobausteine des Zements. Ihre Festigkeit nimmt in Phasen zu. Das abschließende Aushärten dauert Monate.
Tab. 1: Chemische Zusammensetzung von Zementklinker | |||
Bezeichnung | Formel | Symbol | Anteil |
Alit Tricalciumsilicat | 3 CaO · SiO2 | C3 S | 65 % |
Belit Dicalciumsilicat | 2 CaO · SiO2 | C2 S | 16 % |
Aluminatphase Tricalciumaluminat | 3 CaO · Al2 O3 | C3 A | 11 % |
Ferritphase (Brownmillerit) Dicalciumaluminatferrit | 4 CaO · (Al2 O3 , Fe2 O3) | C4 AF | 8 % |
Verringerung von Energieverbrauch und Emissionen
Zementwerke waren immer regelrechte Dreckschleudern, die viel Staub, Abgase, Schwefel, Schwermetalle und andere Gifte in die Umwelt bliesen. Das hat sich in den letzten 30 Jahren grundlegend geändert. 1950 gingen noch 3,5% des in Deutschland produzierten Zementes als Staub verloren. Heute sind es deutlich unter 0,1%. Damals verbrauchten die Zementwerke 7000 Kilojoule Energie je Kilogramm Zement, heute weniger als 2800 kJ/kg. Hochleistungsfilter, energieoptimierte Öfen mit umweltfreundlicher Energieversorgung haben einen sehr hohen Standard.
Darüber hinaus sorgen moderne Zementwerke für aktiven Umweltschutz. Die extrem hohe Flammentemperatur von 2000 °C erlaubt es, beispielsweise Altöl, Haus- und Gewerbemüll, Trockenklärschlamm, Tiermehl und vieles andere zu verfeuern. Dabei entstehen keine zusätzlichen schädlichen Abgase. Altreifen ersetzen mit ihrer Eisenkarkasse sogar teilweise den Primärrohstoff Eisenerz. Weil hochwertiger Kies zur Neige geht, setzt die Betonindustrie im Zuge der Nachhaltigkeit zunehmend Splitt aus Betonabbruch ein.
Weltweit werden mehr als 2,5 Mrd. t Zement jährlich hergestellt, davon in Deutschland 35 Mio. t. Über den Daumen gepeilt, wird je Tonne Zement eine Tonne CO2 emittiert. Für Deutschland liegt der Wert bei etwa 0,7. Die CO2 -Emissionen aus der Zementherstellung entsprechen 2,6% der gesamten CO2 -Emissionen in Deutschland; weltweit sind es etwa 5%. Um die drohenden CO2 -Zertifikatekosten abzuwenden, interessieren sich die Zementwerker für erneuerbare Energien mit ausgeglichener CO2 -Bilanz.
Das größte Potenzial, um die CO2 -Emissionen zu senken, liegt jedoch im Ersatz des Klinkers, der bei Portlandzement 95 bis 100% ausmacht (Tab. 2). So werden in Deutschland mehr als 5 Mio. t Hüttensand (granulierte Hochofenschlacke) verschiedenen Portlandkompositzementen zugemischt. Andere Ersatzstoffe sind z. B. Flugasche (von Steinkohle), die ähnlich dem Puzzolan reagiert, und Kalkstein. Sogar Stroh und Hanf versucht man für spezielle Aufgaben zu nutzen.
Die Entwicklung der Portlandkompositzemente steht erst am Anfang, obwohl ihr Marktanteil mittlerweile schon bei 40% liegt.
Tab. 2: Zusammensetzung wichtiger Zementarten | |||
Art | Benennung | Zementklinker | Weitere Hauptbestandteile |
CEM I | Portlandzement | 95 –100 % | – |
CEM II | Portlandhüttenzement | 65 – 94 % | Hüttensand |
" | Portlandpuzzolanzement | 65 – 94 % | Puzzolane |
" | Portlandflugaschezement | 80 – 94 % | kieselsäurereiche Flugasche* |
" | Portlandölschieferzement | 65 – 94 % | Gebrannter Ölschiefer |
" | Portlandflugasche- hüttenzement | 65 – 79 % | kieselsäurereiche Flugasche*, Hüttensand** |
" | Portlandkalksteinzement | 80 – 94 % | Kalkstein |
CEM III | Hochofenzement | 20 – 64 % | Hüttensand** |
* von Steinkohle ** granulierte Hochofenschlacke |
Beton wird "grün"
Zement und Beton sind im Grunde ideale Kandidaten, um das CO2 -Problem der Welt zu lösen. In fünf Jahren sollen die ersten klinkerfreien "Ökozemente" auf den Markt kommen. Der Rohstoff Kalkstein soll durch Magnesiumhydroxid (Mg(OH)2) ersetzt werden, das durch Kalzinieren (Brennen) bei nur 600 bis 700 °C in Magnesiumoxid (MgO) übergeht. Im Zement wandelt sich dieses bei Wasserzugabe in Magnesiumhydroxid um, das wiederum CO2 aufnimmt. So entsteht das Magnesiumcarbonat Nesquehonit (Mg(HCO3)(OH) • 2 H2 O). John Harrison von der Firma Tececo in Glenorchy in Australien hat eine beeindruckende Rechnung aufgemacht. Um die CO2 -Bilanz der anthropogenen Emissionen auszugleichen, müssten jährlich 12 Mrd. t CO2 gebunden werden. Das lässt sich mit der Erzeugung von 23 Mrd. t Magnesiumcarbonat erreichen. Und dies entspricht der Menge an Beton, die jedes Jahr verbaut wird, nämlich 7 km3 • Ein kleines Problem gibt es aber noch. Der Ökozement braucht ein Jahr zum Aushärten, d. h. zur CO2 -Absorption. Deshalb ist er bisher nicht für den Häuserbau zu gebrauchen. Aber es besteht Hoffnung, Zuschlagstoffe zu finden, die das Aushärten beschleunigen.
Ein ähnlicher Hoffnungsträger ist das Magnesiumsilicat (MgO3 Si) als Klinkerersatz. Es benötigt eine Sintertemperatur von nur etwa 650 °C. Das entspräche zwar einer Emission von 0,5 t CO2 je Tonne Zement. Beim Aushärten baut er jedoch 1,1 t CO2 in die Betonstruktur ein. Ein solcher Zement absorbiert in der Bilanz also ähnlich wie der Ökozement etwa 0,6 t CO2 je Tonne. Aber auch hier dauert das Aushärten bisher zu lange, um damit ein Haus zu bauen.
Korallen als Vorbild
Brent Constantz geht einen ähnlichen Weg. Der Geologe an der Stanford-Universität in Kalifornien hatte sich einst mit Knochenzement befasst. Nun glaubt er, den Stein der Weisen im Meer gefunden zu haben. Er baut gerade in Kalifornien eine Pilotanlage zwischen einem Gaskraftwerk und dem Meeresufer. Sein Konzept hat er den Korallen abgeschaut, die mit Magnesium, Calcium und Kohlensäure ihre Schalen und damit ganze Riffe aufbauen. Er will die kohlendioxidhaltigen Abgase des Kraftwerkes in das Meerwasser leiten. Dort wird das Kohlendioxid in Form von Magnesium- und Calciumcarbonat gebunden, die sich als Carbonatschlamm am Meeresboden absetzen. Der wird geborgen, mit der Abwärme des Kraftwerkes getrocknet und zu Klinker gebrannt, der nicht nur CO2 -neutral ist, sondern auch noch zehn Prozent billiger in der Herstellung sein soll als Portlandzement. Die Klimaberater von Gouverneur Arnold Schwarzenegger sind aber noch skeptisch und warten die ersten Ergebnisse ab, bevor sie das Projekt eventuell unterstützen.
Die richtige Packung macht‘s
Derweil erforscht Franz-Josef Ulm vom MIT in Cambridge (bei Boston) einen anderen Ansatzpunkt. Er hat die Oberfläche vieler Zementarten auf der Nanometerebene mit dem Rasterkraftmikroskop abgetastet und eine überraschende Entdeckung gemacht. In allen Fällen fand er nur zwei Zustandsformen der C-S-H-Partikel. Er nennt die Nanosignatur der C-S-H den Genomischen Code des Zements und schlussfolgert daraus, dass die Festigkeit des Betons nicht vom Mineral abhängt. Vielmehr entscheide die Struktur der gepackten Nanopartikel. Die 5 nm großen C-S-H-Partikel haben nur zwei unterschiedliche Packungsdichten. Ulm vergleicht sie mit Apfelsinen. Entweder liegen sie ungeordnet in einer Kiste, oder sie sind ästhetisch pyramidal aufgestapelt wie bei einem ordentlichen Obsthändler. Die Pyramide führt zu einer wesentlich höheren Packungsdichte mit jeweils mehr Kontakten zu den benachbarten Apfelsinen. Das gilt auch für C-S-H-Partikel und erhöht die Festigkeit des Zements wesentlich.
Ulm sucht nun als Ersatz für den Klinker kostengünstige, ubiquitär verfügbare Mineralien, die dieselbe Packungsdichte des Klinkers erreichen, aber nicht dessen extrem hohe Sintertemperatur benötigen. Das könnte die CO2 -Emission auf ein Zehntel drücken, ist er überzeugt. Zurzeit setzt er ebenfalls auf Magnesium. Und ebenfalls in fünf Jahren will er erste Ergebnisse liefern.
Auf der Nanoebene scheint auch sonst noch einiges möglich zu sein. Seit einem Jahr gibt es einen Zement mit zugemischtem nanokristallinem Titanoxid. Das Molekül oxidiert photokatalytisch Stickoxide der Luft zu Nitrat. Das ist ein aktiver Beitrag der Pflastersteine gegen Sommersmog.
Fazit: Zement wird immer besser. Es gibt über 30 Arten, und es werden immer mehr. Irgendeiner wird die Welt retten.
Zement im NetzVerein Deutscher Zementwerke e. V. Initiative für Nachhaltigkeit in der Deutschen Zementindustrie www.initiative-nachhaltigkeit.de Virtuelle Zementfabrik www.juracement.ch/virtfabrik/flash/virtfabrik.html Deutsches Zementmuseum Hemmoor Fachbegriffe werden erklärt |
Literatur
Georgios Constantinides, Franz-Josef Ulm: The nanogranular nature of C-S-H. Journal of the Mechanics and Physics of Solids 55, 2007, 64-90.
Ralf Löckner, Birgit Timmer: Nachhaltigkeit und Zementindustrie – Dokumentation von Beiträgen und Handlungsoptionen. Bau + Technik, Düsseldorf 2002.
Autor
Dr. Uwe Schulte,
Händelstraße 10,
71640 Ludwigsburg,
schulte.uwe@t-online.de
0 Kommentare
Das Kommentieren ist aktuell nicht möglich.